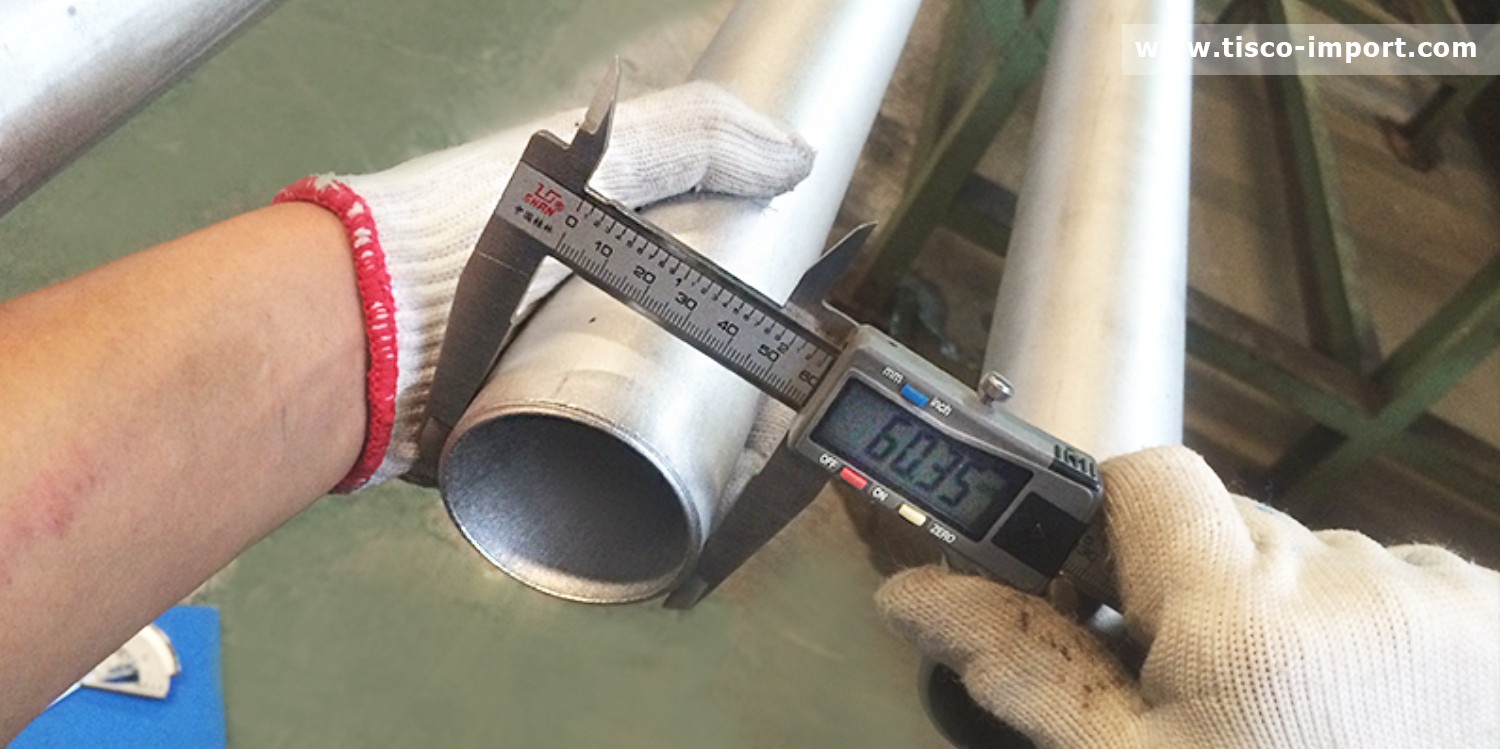
Inspekcja towaru w trakcie produkcji, zaraz po inspekcji przedwysyłkowej, jest drugim najczęściej stosowanym rodzajem kontroli jakości w imporcie z Chin. Kontrola podczas produkcji pozwala wykryć wady produktów już na początkowym etapie ich powstawania. Co z kolei bardzo skutecznie zapobiega dodatkowym kosztom jak i opóźnieniom w dalszej produkcji i wysyłce. Im wcześniej wady jakościowe zostaną wykryte, tym lepiej dla naszego zamówienia. Ponieważ na tym etapie ilość towarów wyprodukowanych z defektem jest stosunkowo mała, możliwa jest wymiana i szybkie wdrożenie poprawek do produkcji masowej.
Chociaż kontrola jakości podczas produkcji może wydawać się podobna do inspekcji materiałów i komponentów przed produkcją, czy inspekcji przedwysyłkowej, istnieją pewne wyraźne różnice. Inspekcja podczas produkcji, jest niezbędna dla minimalizacji ryzyka opóźnień, nierzadko pojawiających się w imporcie z Chin. Poza opóźnieniami podczas Chińskiego Nowego Roku, najczęszciej spotykaną przyczyną opóźnień w produkcji i wysyłce jest konieczność naprawy lub ponownej produkcji wadliwych towarów. Tak więc wczesne wykrycie wad jest podstawą do zapewnienia terminowej realizacji zamówienia. Inspekcja podczas produkcji jest w szczególności ważna dla produktów wytwarzanych według indywidualnej specyfikacji importera (produkcja OEM oraz ODM). Inspekcja podczas produkcji, w zależności od wielkości zamówienia, zajmuje od jednego do kilku dni, podczas gdy monitoring produkcji polega na codziennej kontroli całego procesu produkcyjnego.
Dlaczego inspekcja podczas produkcji jest ważna?
Zdarza się, że jakość całej partii produkcji, dla danego zamówienia odbiega od ustalonych standardów. Do problemów jakościowych mogą należeć: źle nadrukowane logo, za małe oznaczenie CE, błędy w polskiej pisowni na metkach czy etykietach, niezgodność z parametrami takimi jak: wymiary, kolor, waga, moc, wytrzymałość, twardość, ścieralność, skład chemiczny itp. Wykrycie tego typu wad podczas inspekcji przedwysyłkowej stanowi duży problem zarówno dla importera jak i dla fabryki. Na tym etapie zamówienie powinno być już gotowe do wysyłki, natomiast konieczne poprawki czy ponowna produkcja wszystich towarów może zająć kolejny miesiąc. Dodatkowo ponowna produkcja wiąże się z dużymi kosztami. W związku z tym dostawca może zarządać dopłaty do zamówienia na pokrycie kosztów materiałów i siły roboczej. Warto więc, w planie kontroli jakości dla swojego zamówienia, uwzględnić również dodatkową inspekcję podczas produkcji.
Celem inspekcji w trakcie produkcji jest jak najwcześniejsze rozpoznanie wad i problemów w produkcji masowej. Wczesne wykrycie defektów jest bardzo istotne ponieważ:
- Małą część wyprodukowanych już towarów, dla których wykryto wady jakościowe, często można naprawić lub wyprodukować ponownie bez powodowania opóźnienia i generowania dodatkowych kosztów
- Wczesne wykrycie problemów pozwala nie tylko na na szybkie wprowadzenie procedur naprawczych, ale również na uniknięcie powtarzających się defektów dla pozostałej części produkcji
Jeśli problemy z jakością zostaną wykryte na wczesnym etapie, importer powinien zarządać od dostawcy pracy nad planem działań naprawczych. Inspekcja podczas produkcji, jest sposobem na wykrycie i udokumentowanie problemu z jakością. Dzięki temu można zlecić fabryce działania naprawcze. Dodatkowo, inspekcja podczas pierwszej produkcji, pozwala lepiej zrozumieć dostawcy wymagania importera. Rozpoznanie wady i wdrożenie procedur naprawczych, pozwoli również uniknąć problemów z jakością, w przypadku powtarzających się przyszłych zamówień.
Dlaczego warto wybierać firmę kontrolującą jakość zlokalizowaną w Chinach?
Każdy importer przy zamawianiu produktów z Chin, powinien liczyć się z ryzykiem jakie podejmuje. Kwestie takie jak różnice kulturowe i bariery językowe mogą utrudniać współpracę z producentami. Dlatego warto zlecić kontrolę jakości firmie, która funkcjonuje na chińskim rynku i specjalizuje się w tego typu usługach. Firma, kontrolująca jakość produktów w fabryce na zlecenie zagranicznego klienta, powinna być jednocześnie skutecznym pośrednikiem między obydwoma stronami.
Zwłaszcza teraz, przy tak wielu ograniczeniach dotyczących podróży i handlu, ważne jest, aby mieć swojego przedstawiciela w Chinach. Pozwala to na skutecze zarządzanie zamówieniem, sprawdzenie czy produkcja realizowana jest prawidłowo oraz daje większą kontrolę nad terminem wysyłki. Współpraca z pośrednikiem handlowym, daje dodatkowe poczucie bezpieczeństwa, minimalizując ryzyko błędów i opóźnień.
Kiedy należy przeprowadzić inspekcję podczas produkcji?
Idealny czas na przeprowadzenie inspekcji podczas produkcji w rzeczywistości zależy od rodzaju produktu i doświadczenia fabryki. W większości przypadków najlepiej jest przeprowadzić inspekcję podczas produkcji, gdy wyprodukowano od 20% do 40% towarów. Inspekcja na tym etapie pozwala uniknąć zarówno problemów z jakością na początku produkcji jak i opóźnień pod koniec. Zwłaszcza w przypadku wykrycia problemów, wobec których producent będzie potrzebował planu działań naprawczych.
Jeśli importer zdecyduje się czekać, aż 50% towarów zostanie ukończonych, prawdopodobnie kolejne 30% jest już przetwarzanych. Jeśli na tym etapie zostaną wykryte problemy z jakością, mogą one występować już w 80% towarów z zamówienia! Niemniej jednak, dopuszcza się stosowanie inspekcji podczas produkcji w przypadku ukończenia 80% towarów, jeśli następujące warunki są spełnione:
- Fabryka ma duże doświadczenie w wytwarzaniu danego rodzaju produktu, pry określonym stopniu zaawansowania,
- Czas cyklu, potrzebny do wyprowadzenia pierwszych gotowych produktów z linii produkcyjnej nie przekracza 10 dni.

W związku z przeprowadzaniem inspekcji w trakcie produkcji istnieją dwa kluczowe zagrożenia, których należy unikać.
Zbyt wczesne przeprowadzenie kontroli jakości
Pierwsze produkty, które schodzą z linii produkcyjnej, nie odzwierciedlają średniej jakości całej partii. Zwykle są gorsze. A fabryka powinna mieć czas, również na wewnętrzną kontrolę jakości. Dodatkowo, jeśli koniecznie chce się sprawdzić produkty, które przeszły już kilka etapów produkcji, ale nie zostały jeszcze w pełni ukończone, najpierw należy upewnić się, że na obecnym etapie można wykryć problemy z jakością. Każdy produkt ma inną specyfikę, dlatego też moment przeprowadzenia kontroli jakości, zależy między innymi od rodzaju produktu.
Zbyt późne przeprowadzenie kontroli jakości
Większość fabryk w Azji produkuje towary w bardzo dużych partiach. Z tego powodu gotowe produkty często pojawiają się w dużych ilościach, dopiero po upływie dłuższego czasu od rozpoczęcia produkcji. Zdecydowanie utrudnia to kontrolę jakości mniejszych partii gotowych produktów na początkowym etapie produkcji. W tym przypadku warto rozważyć kontrolę poszczególnych etapów produkcji.
Co jest sprawdzane podczas produkcji?
Inspektor sprawdza przede wszystkim, czy produkcja odbywa się we właściwej fabryce, a nie zlecana jest podwykonawcom. Może również poprosić o zaktualizowany plan produkcji. Następnie przechodzi do sprawdzenia zgodności produktu ze specyfikacjami i/lub złotą próbką.
Podczas kontroli jakości, inspektor pobiera próbki gotowych towarów, zwykle w oparciu o międzynarodową normę ANSI / ASQC Z1.4 (ISO2859-1), jeśli zleceniodawca nie postanowił inaczej. Czynności jakie wykonuje inspektor podczas inspekcji, są następujące:
- Przeprowadzenie oceny jakości wybranych towarów, zgodnie z regułami próbkowania względem dopuszczalnego poziomu jakości (AQL);
- Sprawdzenie opakowań i etykiet;
- Zweryfikowanie liczby gotowych produktów;
- Zbadanie sytuacji produkcyjnej i terminowości wysyłki względem wymagań klienta;
- Sprawdzenie, czy reszta towaru jest możliwa do zidentyfikowania w trakcie procesu produkcyjnego;
- Przetestowanie gotowych produktów pod kątem bezpieczeństwa, trwałości, wydajności i funkcji.
Inspekcja podczas produkcji może zakończyć się niepowodzeniem z trzech powodów:
#1 Niezgodność ze specyfikacją
Wszystkie istotne aspekty produktu (ilość, komponenty, montaż, estetyka, funkcja, rozmiar, etykietowanie itp.) są kontrolowane w oparciu o wymagania nabywcy.
#2 Zbyt wiele wad wizualnych
Na podstawie planu pobierania próbek inspektor wybiera i sprawdza niektóre produkty, a następnie porównuje liczbę defektów z limitami AQL lub wcześniejszymi ustaleniami między importerem, a fabryką.
#3 Niepowodzenie testów
Inspektor może wykonać kilka prostych testów w fabryce (zamiast wysyłać próbki do laboratorium). Na przykład, pełna kontrola funkcji, aby upewnić się, że dany produkt w pełni i sprawnie działa.
Jakie ograniczenia wiążą się z kontrolą jakości podczas produkcji?
1. Sama kontrola jakości podczas produkcji, nie jest wystarczająca, aby upewnić się o jakości całego zamówienia. O ile takie działanie pomaga wykryć defekty i wdrożyć procedury naprawcze, to nie daje gwarancji, że fabryka zastosuje się do procedur i nie popełni więcej tych samych błędów. Inspekcja podczas podukcji nie daje również informacji o ewentualnych problemach dla kolejnych partii produktów. Z racji tego, że chwalenie się wadami nie leży w interesie fabryki, zapewne nie poinformuje ona nabywcy o późniejszych wadach, z zamiarem przyszłej wysyłki wadliwego towaru. Dlatego, po kontroli podczas produkcji powinno przeprowadzić się wyrywkową, przedwysyłkową kontrolę, potwierdzająca średnią jakość całego zamówienia.
2. W przypadku skomplikowanych lub nowych projektów fabryka może potrzebować wskazówek od importera już na samym początku produkcji. Jest to zatem praca dla nabywcy, odpowiedzialnego za skonfigurowania procesów zgodnie z wymaganiami. W tym przypadku nabywca albo wysyła swoich techników do fabryki producenta w Chinach albo zleca to zadanie lokalnym firmom specjalizujących się w sprawach jakości. Takie działanie pozwala przeszkolić personel fabryki, jak wytwarzać produkt, według standardów nabywcy. Jednak taka opcja sprawdza się zazwyczaj tylko we współpracy z małymi fabrykami, które mają niewielu pracowników. Interwencja w procesy dużych fabryk, może być nieskuteczna.
3. W niektórych przypadkach produkcja odbywa się na wielu liniach produkcyjnych lub nawet w wielu fabrykach. Wówczas, jeden inspektor nie będzie w stanie, w ciągu jednego dnia sprawdzić średniej jakości produktów. Procesy prodykcyjne niektórych towarów, jak na przykład maszyn są bardzo złożone. Najpierw produkuje się poszczególne komponenty i części, a na końcu składa się kompletną maszynę. Dla takiego produktu jedniodniowa kontrola podczas produkcji nie wystarczy, aby dostatecznie sprawdzić jakość. Podobnie, podczas kontroli przedwysyłkowej należałoby rozłożyć całą maszynę, aby upewnić się o finalnej jakości całego produktu. Dlatego, w takim przypadku, jeśli mamy do czynienia z bardziej wymagającym produktem, zaleca się przeprowadzić codzienną kontrolę procesu produkcji czyli tzw. monitoring produkcji.
4. W wielu przypadkach na etapie produkcji nie ma jeszcze możliwości sprawdzenia oznakowania opakowań pojedyńczych i zbiorczych. Chińskie fabryki zwykle otrzymują opakowania pod koniec produkcji, intencjonalnie opóźniając płatność za materiały oraz oszczędzając miejsce w swoim magazynie. Dlatego też i w tym przypadku zaleca się przeprowadzić dodatkową inspekcję przedwysyłkową.
Korzyści płynące z kontroli jakości przeprowadzonej przez firmę zewnętrzną
Znaczna część fabryk w Chinach posiada własny, wewnętrzny dział kontroli jakości, który odpowiedzialny jest za wyrywkowe sprawdzenie produktów. Wewnętrzna kontrola, którą przeprowadza fabryka nie jest jednak żadną gwarancją jakości dla importera. Podczas takiej kontroli, fabryka ma bardzo duże możliwości manipulacji. Procedury kontrolne jak i standardy ich wykonywania narzucane są przez fabrykę i są takie same dla wszystkich produktów, zarówno tych docelowo produkowanych na rynek Chiński, Afrykański jak i Europejski. Tak więc wewnętrzna kontrola przeprowadzana przez fabrykę nie uwzględnia indywidualnych wymagań importera. Co więcej, to fabryka wybiera konkretne próbki do kontroli. Testy kontrolne z kolei przeprowadzają pracownicy fabryki, którym zależy, aby wynik kontroli był jak najlepszy.
To w odpowiedzialności importera leży dokładne sprawdzenie, czy towar produkowany przez dostawcę spełnia wymagane standardy. Najlepszym sposobem na upewnienie się o jakości produktów jest zlecenie kontroli jakości niezależnej firmie zewnętrzej, a nie pracownikom fabryki. Kontrole jakości wykonywane przez niezależnych inspektorów z firm zwenętrznych, mają wiele zalet, które mogą nie być widoczne na pierwszy rzut oka. Przede wszystkim są one niezależne i jawne. Inspektorzy zewnętrzni, zatrudniani są przez importera, tak więc reprezentują oni interesy klienta, a nie fabryki. Inspektor na podstawie specyfikacji technicznej i planu inspekcji, dostarczonych przez importera dokonuje konroli jakości. Proces kontroli jak i osiągnięte wyniki są jawne zarówno dla importera jak i dla fabryki.
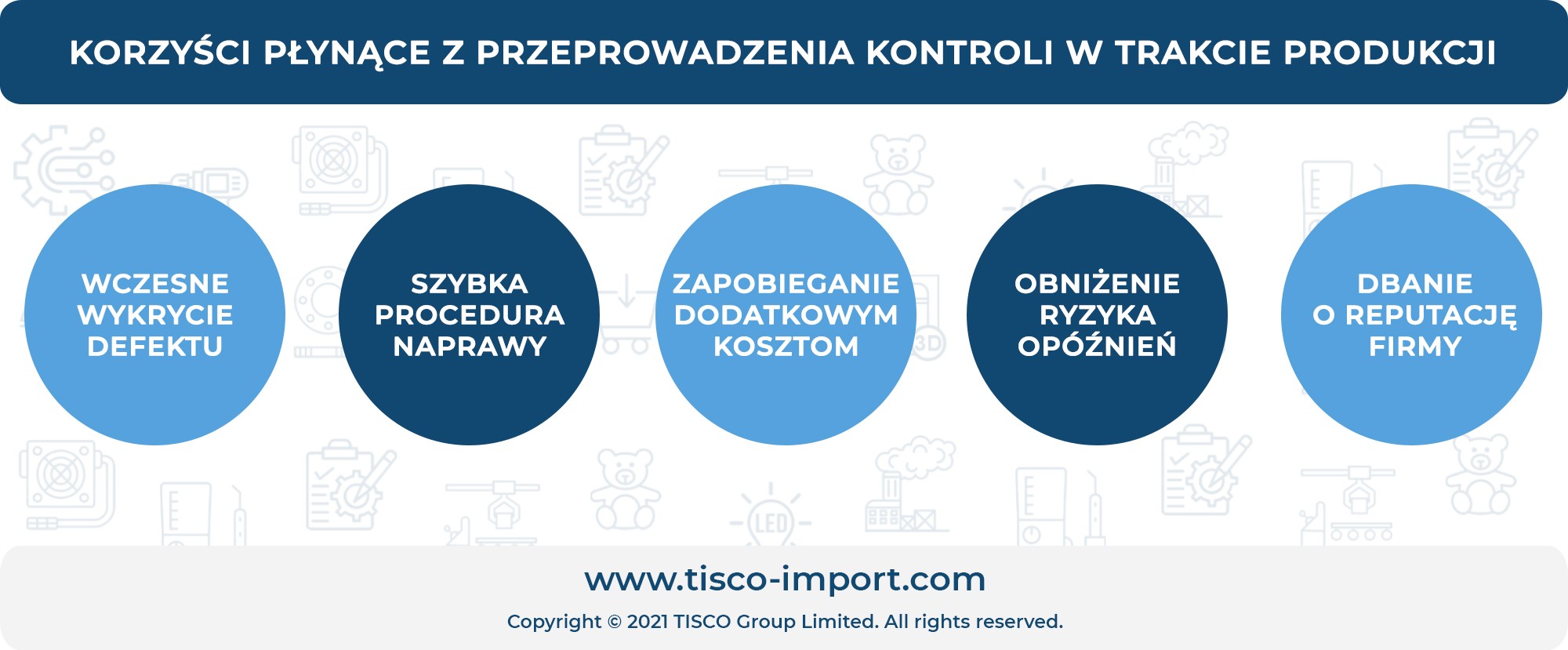
Podsumowanie
Może się wydawać, że fabryki w Chinach nieustannie wizytowane są przez zewnętrznych inspektorów w celu przeprowadzenia kontroli jakości czy to przed, w trakcie czy po produkcji. Niemniej jednak te kontrole są niezbędne, aby upewnić się, że zarówno proces produkcji, jak i sam produkt odpowiadają wymaganiom jakości. Fabryki, którym zależy na dostarczeniu właściwych produktów i rozwinięciu długotrwałej współpracy mają pozytywne nastawienie do zewnętrznych kontroli jakości. Dzieje się tak, ponieważ w długotrwałej współpracey, zewnętrze kontrole jakości działają na korzyść obu stron. Im wcześniej defekt zostanie wykryty, tym mniejsze ryzyko opóźnień i dodatkowych kosztów. Jeśli niezgodności, nie zostaną wykryte wystarczająco wcześnie, importer może być narażony na ogromne straty finanoswe i reputacyjne. Problemy związane z wyprodukowaniem towaru niespełniającego założonych standardów jakości, zwykle kosztują znacznie więcej, niż dzień pracy inspektora, który może uratować realizację zamówienia i renomę firmy.